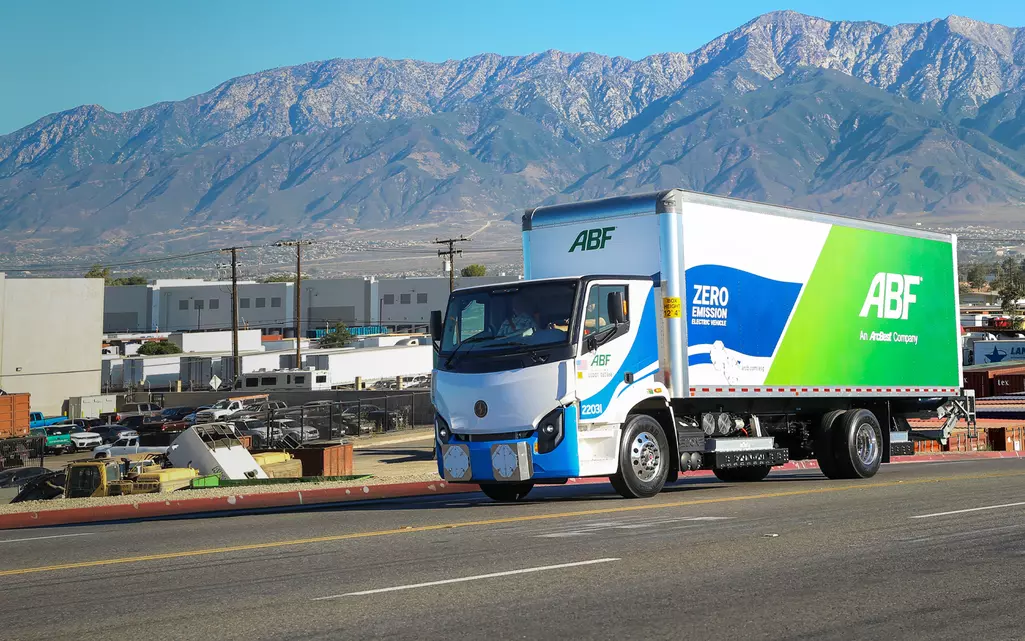
Our Environmental Focus
Taking action to create a
healthier workplace,
industry and world
ArcBest is Committed
ArcBest is committed to ongoing improvements and responsible environmental management. We’re focused on enhancing the efficiency of our equipment, facilities and logistics operations and on transparently monitoring our performance through regular reporting.
Greenhouse Gas Emissions
We began disclosing our Scope 1 and Scope 2 greenhouse gas (GHG) emissions in 2022 and are making meaningful progress toward reporting our Scope 3 GHG emissions.
2024 GHG Emissions Data*:
*Emissions calculated using US EPA Factor Hub, published September 2023
Environmental Focus Areas
Equipment
We’ve been mindful of using more efficient equipment in our ABF Freight fleet for over 50 years — strategically investing in cleaner, more modern trucks each year to replace older units and reduce our carbon footprint. According to one S&P Global stat, today’s clean diesel trucks produce 99% fewer emissions than those on the roads in the 1980s. Our trucks are also equipped with low-rolling resistance tires to reduce energy loss and improve fuel efficiency.
Investing in electric vehicles (EVs) is another ongoing initiative. With thirteen EVs currently in our fleet, we’re continuing to monitor impact to determine the best fit in our LTL network.
Facilities
We operate out of 250 campuses and service centers across North America. As we build new facilities and make updates, we’re making responsible decisions that are good for the environment and for our people. Upgrades include:
- Converting to LED and motion-sensor lighting
- Replacing HVAC units with high-efficiency units
- Installing water-efficient plumbing
- Purchasing office furniture manufactured from sustainable materials
- Updating employee common areas to improve comfort, safety and appearance
Operations
ArcBest owns and operates over 40,000 assets across our ABF LTL network. Recognizing the impact this can have on the environment, we continually analyze our operations to create more efficient routes that eliminate unnecessary miles and reduce fuel usage.
One solution: City Route Optimization — technology that our expert teams developed using artificial intelligence and historical data — creating the optimal route structure throughout ABF’s LTL network. To date, this innovation has delivered:
- 1.5% increase in street productivity
- 17% reduction in using local cartage agents
- A cost savings of over $25.8 million
Compliance
Across our 240 ABF service centers, we comply with all environmental regulations to protect our communities, people and natural resources. Our approach includes stormwater pollution prevention measures per the EPA Clean Water Act, ensuring all service centers are either stormwater permitted, have a No Exposure Certification or are exempt.
We also meet fuel and oil storage standards by using advanced tank systems and EPA-compliant spill prevention plans to protect water sources. Our aboveground and underground tanks comply with federal, state and local regulations. We have both double-walled and single-walled underground tanks — the double-walled tanks are comprised of either fiberglass-clad steel or fiberglass-reinforced plastic, and the single-walled tanks are made of either steel or fiberglass-reinforced plastic. Both types have spill and overfill prevention and electronic monitoring capabilities. Additionally, we minimize waste by recycling oil, antifreeze, cleaning solutions and scrap metal and use sustainable alternatives like cloth rags.
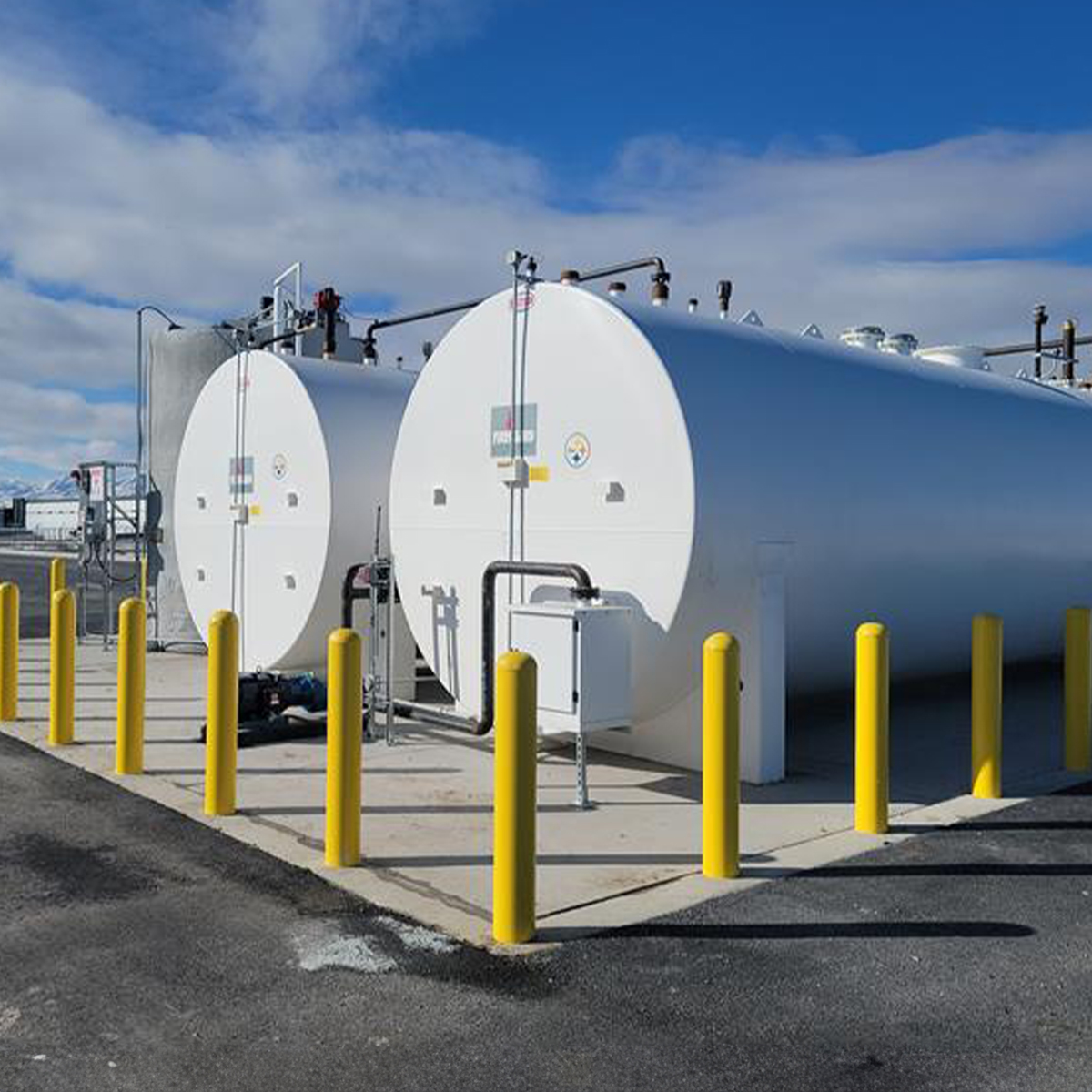